
Ultrasonic piezoelectric linear motors are useful where both large travel ranges and high speeds are required, even to 500 mm/sec. With each oscillatory cycle, the mechanics smoothly executes a step of a few nanometers. Through its contact with the friction bar, it provides micro-impulses and drives the moving part of the mechanics (slider and turntable) forward or backwards. An alumina friction tip (pusher) attached to the plate moves along an inclined linear path at the eigenmode frequency. A rectangular monolithic piezoceramic plate (the stator) is segmented on one side by two electrodes.ĭepending on the required direction of motion, one of the electrodes of the piezoceramic plate is excited to produce high-frequency eigenmode oscillations (one of the normal vibrational modes of an oscillating system) of tens to hundreds of kilohertz. In ultrasonic piezoelectric motors, the piezoelectric ceramic material produces high-frequency acoustic vibrations (inaudible to the human ear) on a nanometer scale to create a linear or rotary motion. Both of these devices are called piezomotors, and both basically provide unlimited travel. To produce longer travel, one of two clever arrangements is used - either running a single piezoelement at its resonant frequency, or operating multiple actuators together. Piezoelectric actuators in their basic form provide very small displacement.
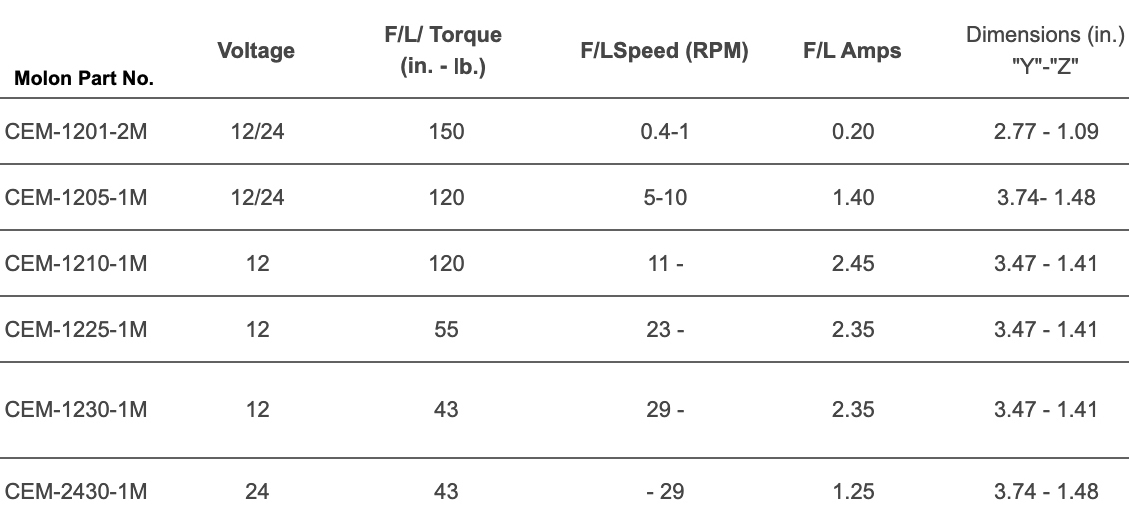
The name derives from the Greek word piezein, meaning to squeeze or press. The use of piezoelectric materials dates back to 1881 when Pierre and Jacques Curie observed that quartz crystals generate an electric field when stressed along a primary axis. These motors are improving performance in medical applications.
PIEZO ACTUATORS IN VENDING MACHINE DRIVER
Then high electric fields are used to align material domains along a primary axis and induce polarization.Ĭeramic-encapsulated piezo stacks can be used in precision valves.ĭesign options include miniature piezo ceramic rotary stages, linear stages, and pushers.Ī miniature piezo linear motor slide with on-board driver can reach velocities of 200 mm/sec. Piezoelectric ceramics consist of ferroelectric materials and quartz: High-purity PZT ( plumbum, zirconate, titanate) powders are processed, pressed to shape, fired, and electroded. In short, a piezoelectric ceramic element produces mechanical energy in response to electrical signals, and conversely, produces electrical signals in response to mechanical stimulus.
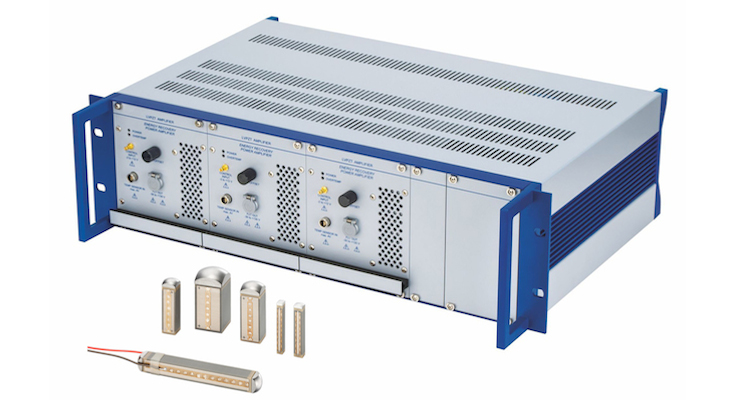
Piezomotor definedĪ piezoelectric or piezo actuator is a solid-state actuator that leverages the shape change of piezoelectric material when an electric field is applied. In the same way, recent advancements in piezoelectric motors and actuators are spurring other new designs. OFDI operates at several magnitudes of improvement over its predecessor, optical coherence tomography, in turn enabled by laser-scanning advancements 15 years ago.
PIEZO ACTUATORS IN VENDING MACHINE SERIAL
Consider medical-instrument manufacturing: The research, design, modeling, testing, prototyping, and FDA and EU approvals of new mechatronic devices, or the integration of changes to existing designs, usually represents a sizable capital investment well before the equipment goes into serial production.Ī key impetus for medical and bioresearch companies is to capitalize on technological advances for the manufacture of better, more efficient equipment: A recent improvement in high-speed laser scanning, for example, spurred Harvard Medical School's latest imaging technique, optical frequency-domain imaging or OFDI, which is capable of visualizing a patient's coronary arteries in unprecedented 3D detail. Motion-device functionality is influenced by a myriad of design requirements. The atomizer head of the eFlow Rapid Electronic Nebulizer employs an annular ultrasonic piezo transducer. Preumont A (1997) Vibration control of active structures.A piezoelectric microscope nanofocusing device - called a Z motor - provides 10 times faster response and resolution than classic motor-driven units. Publicis MCD Verlagīrecher C (2002) Vergleichende analyse von Vorschubantrieben für Werkzeugmaschinen. Groß H, Hamann J, Wiegärtner G (2000) Elektrische Vorschubantriebe in der Automatisierungstechnik. (2009) Technische Dokumentation Servosystem S1. Neugebauer R, Bucht A, Illgen A, Wittstock V (2007) Schwingungsreduktion mit Aktor-Sensor-Einheiten. Neugebauer R, Wittstock V, Illgen A, Naumann G (2006) Piezo-based actuator-sensor-units for uniaxial vibration reduction in machine tools.
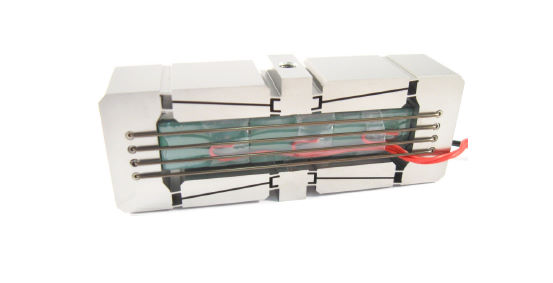
Lenk A, Pfeifer G (2001) Elektromechanische systeme. Jendritza D (1998) Technischer Einsatz Neuer Aktoren. Verlag Wissenschftliche Scripten, Zwickau
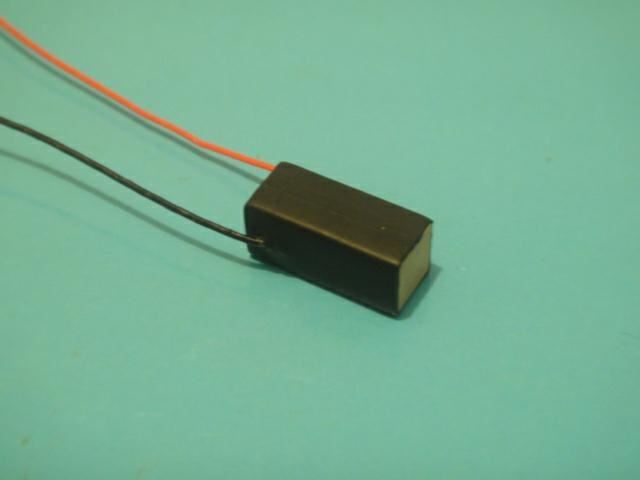
Wittstock V (2007) Piezobasierte Aktor-Sensor-Einheiten zur uniaxialen Schwingungskompensation in Antriebssträngen von Werkzeugmaschinen. Wittstock V (2006) Entwicklung piezobasierter Komponenten für den Maschinenbau.
